目录
**章 离心法发展史 1
第二章 流体及颗粒在离心立场中的运动 3
2.1转鼓内液体的自由表面 3
2.2转鼓内液体的压力 4
2.3颗粒在离心力场中的运动——离心机分离性能预测 5
第三章 沉降离心机 9
3.1沉降式离心机工作原理 9
3.2沉降式离心机 10
参考文献: 17
**章 离心法发展史
人类很早就发现,利用引力场可以分离不同分子质量的物质,并在淘金等技术中应用这种方法.利用引力场分离不同分子量的气体已有近百年的历史.早在1895年,德G的布雷迪克(Bredig)shou先利用这种方法分离了混合气体。后来,当发现了元素存在不同的同位素以后,很快就有人利用引力场来分离了同位素。1919年,林德曼(Lindemann)和阿斯顿(Aston)指出:若在地面和三万米的高空分别对空气取样,则样品的氖同位素组成将有明显差别。并认为在实际工作中**有希望的分离方法是采用气体离心机,但是都未获得成功。知道1934年,美G弗吉尼亚大学学者比姆斯(Beams)shou先研制成功了能分离气体同位素的离心机,并实现了氯同位素的分离。**此,用离心机来分离同位素在理论和实验上都初步得到了验证。当采用离心法分离不同分子量的气体时,其分离效应仅取决于两种气体分子量之差,而与气体平均分子量的大小无关。也就是说,离心不像气体扩散法等一些其他分离方法那样,分离效应会随着气体平均分子量的增大而减小。因此拥立新发来分离同位素是特别适合的。在第二次世界大战期间,一些G家开始研究生产核武器用的浓缩铀的方法,离心法被公认为是一种有希望的方法。于是,离心法研究工作进入了分离铀同位素的阶段。shou先探索用气体分离机来分离铀同位素的是美G,在比姆斯研究工作的基础上,他们改进了分离机,shou先实现了铀同位素的分离。伺候,他们根据热扩散等分离方法中提出了多极化原理,成功的研制了利用轴向逆流方式使分离效应得到倍增的逆流的离心机,使离心机取得了很好的分离效果。但是,由于工程技术上的原因,无论是单台离心机的分离能力。还是离心机的运行可靠性,都还无法达到工业生产的要求,工作只停留在实验室研究阶段。
五十年代起,离心法分离铀同位素的研究工作集中在离心机机型的研制方面,目前是研究满足工业生产的具有一定分离能力的离心机。在这方面做出贡献的主要是德G科学家,其中**的有苏联呢、联邦德G和美G从事研究的齐佩(Zippe)和在伯恩大学从事研究的柏罗特(Groth)。他们分别研制成了两种不同类型的分离机,在本节后面将对他们做专门介绍。其中齐佩研制的离心机**富有创造性,一起简单而独特结构满足了工业用离心机长寿命低能耗的要求,吧离心法研究工作向前推进了一大步,为离心法在实验室研究向生产规模做出了重要贡献。
六十年代中期,由于核电站的迅速发展,对核燃料的需要量激增,加上齐佩离心机为了工业化奠定了基础,分离法研究工作引起了更多G家重视,并有了很大的发展。研究的*域从单台离心机逐渐扩大到级联装置和小型试验工厂。在单机研究方面,为了增加分离能力采用了新的高强度转子材料,是离心机在更高圆周运动转速下运行,同时不断增加转子长度,这些为了离心法在工业应用创造了更有力的条件。在这个阶段中,西欧的英G、联邦德G、荷兰三G处于**地位,它们于1974年分别创建了三座年分离功为二十吨左右的离心试验工厂,成功生产了低浓铀。
七十年代后期,离心法生产浓缩铀开始进入成熟阶段。离心机性能的不断改进和试验工厂的顺利投产证明了离心法可以再经济性方面与气体扩散法相竞争,成为以工业规模生产弄所有的新方法。根据目前各G公布的计划来看,在近期拟建的新浓缩铀工厂中,英G、联邦德G、日本等G都选择了离心法。1980年英G、联邦德G、荷兰三G合作建成了两座年分力功为200t离心示范工厂。到1985年这两座工厂总的分离功已扩大到约1500t,计划到八十年代末再把分离能力增加一倍。日本在建成离心实验工厂,于1984年开始建设年分离功为200t的离心示范工厂。美G政府曾于1977年决定本G第四个浓缩工厂采用离心法。伺候,他们加强了离心法及有关技术的研究工作,于1983年建成了年分离量为23t的离心示范工厂,并继续进行先进的大型离心机的研究工作。后由于激光分离法的进展和浓缩铀大量过剩等种种原因,于1985年决定停建离心浓缩工厂。
在离心法分离铀同位素的发展过程中,理论工作也占有相当重要的地位。早期在分离理论方面做出贡献的有马丁(Martin)、科恩(Cohen)等人。尤其是美G学者科恩,他以热扩散柱分离理论为基础,**早对各种类型离心机的分离性能进行了比较系统的分析,初步建立了离心法的基本理论。此后,离心分离理论的研究工作不断深入、随着离心法从实验室向工业规模过度。近年来,有关离心法的研究报告陆续发表,大大扩展和丰富了离心分离理论的内容。
第二章 流体及颗粒在离心立场中的运动
转鼓内液体的自由表面#p#分页标题#e#
离心机开动后,因转鼓的带动,使转鼓内液体在受重力作用的同时,还受到离心力的作用,形成一个旋转的自由表面(如图)
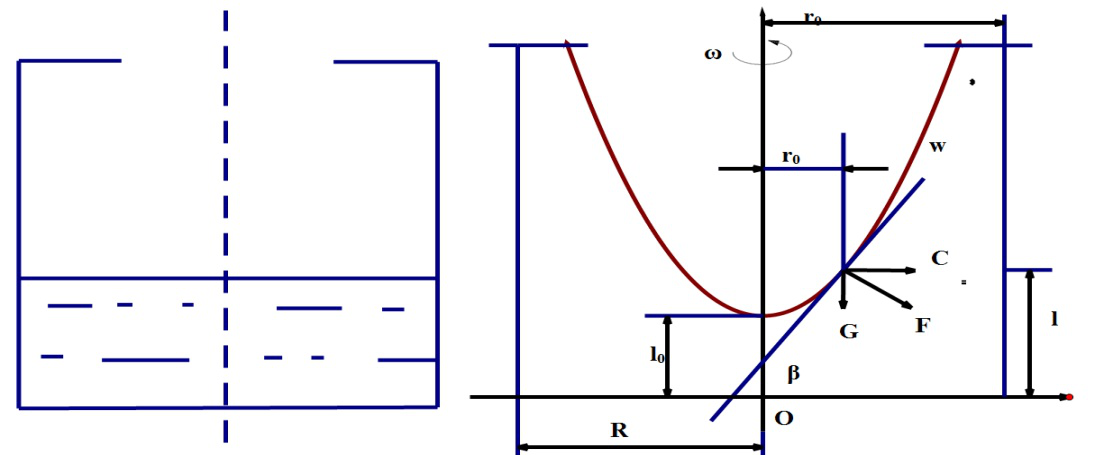
a.静止 b.低速
c.高速 d.忽略重力
在自由液面上任取一单元体(如b),其质量为dm,回转半径(所处径向位置)为r
0,离鼓底的高度为l,设转鼓的旋转角速度为ω,则此单元所受的离心力C和重力G分别为:
这两个力的合力F的方向应垂直于该点自由液面的切线,故:
积分,得
由此可见,液体的自由表面为一旋转抛物面。
当转速增大时,抛物面逐渐下凹,甚**可能< 0(如c);同时,周围液体上升。因此,实践中为防止液体溢出,转鼓顶部应设一定高度的溢流堰,只让一定量的液体(澄清液)溢出。
当转速极大,以**重力相对于离心力可忽略不计时,则自由液面趋近于圆柱面,即r
0 = R
0 = (如d)。
2.2转鼓内液体的压力
在鼓内物料中任取一单元体或微分体积:
因其角速度ω旋转运动,故旋转产生的离心力为:
微分体积上压力的径向平衡条件为:
忽略二次项,化简得
参考图b沿径向对上式积分,得
这是物料中某一径向位置有离心作用产生的离心压力,式中r
0为自由液面的径向位置。由此可见,在水平面内,离心压力是径向位置的函数,在鼓壁处达到**大值:
另外,在一般情况下,由于随轴向位置而变,所以沿鼓壁的不同高度处,鼓壁所受的离心压力是不同的。由图b可看出,当=0时,离心压力达到**大值:
当< 0时,离心压力的**大值发生在靠近鼓底的鼓壁上。
实际上,在离心机的正常操作条件下,因重力影响课忽略,所以r
0沿轴向课认为是常数,从而离心压力沿轴向也可近似的看作常数。因此,上述情况(r
0常数)仅适用离心机的启动、停车等非正常情况。
计算离心压力的意义在于确定转鼓的离心应力,同时,由于离心压力是离心操作的驱动力,因此,离心压力也是离心过滤操作的设计基础。
颗粒在离心力场中的运动——离心机分离性能预测
离心机转鼓的高速旋转,带动了转鼓内液体和颗粒的高速旋转,于是,颗粒就作离心沉降运动。在分析颗粒的运动的时,作如下解释:
1、 由于离心力与重力之比(分离因素)很大,因而足以克服颗粒的布朗扩散力;
2、 虽然有些大颗粒可能

>1(即过渡区甚**湍流区),但它们往往总是以100%的效率被分离。也就是说,离心机的分离效率主要决定于小颗粒的分离特性。因此,离心机分离性能的分析是以小颗粒(即

<1)的斯托克斯沉降为基础的;
3、 先以结构简单的管式离心机(离心力和重力之比——分离因数很大)的分析着手,即重力影响忽略不计,鼓内液体自由面为圆柱面。这种分析方法,稍加修正就能用于其他类型的离心机;
4、 忽略干扰沉降;
5、 忽略哥氏力;
6、 除上述简化外,忽略颗粒的加速时间,即假定颗粒加速到终了沉降速度是瞬时即达
虽然上述建设显得有些过分简化,但由于离心机内流动的低湍流特性,**后的分析结果还是能比较合理地反映离心机的性能。
这样,颗粒的沉降速度(径向)为:
其中:
式中

——离心加速度;

——颗粒所在的径向位置
由式得
假定颗粒从某一径向位置r开始沉降,一直到壁面,即径向位置R,则颗粒完成沉降所需的时间为:
由上式知,颗粒完成沉降所需的时间是其径向位置#p#分页标题#e#

的函数。颗粒是否能完成沉降——达到径向位置R,一方面决定于颗粒所处的其实径向位置,另一方面还决定于颗粒在转鼓内的允许的停留时间,或平均停留时间

。

怎么计算呢?shou先,为简便起见,作如下假设:
1、 液体的轴向运动为柱塞流,即沿转鼓横截面的液流速度均匀分布,并忽略端效应的影响
2、 颗粒与液体具有相同的轴向速度
由图可知,流体的通流面积为

(

-

)。若通过离心机的流量为Q,则流体的平均轴向速度为:
颗粒在转鼓内的停留时间为:
式中

(

-

)

为流体的体积,成为转鼓的有效容积,用

表示,则:
由上述可知,处理量Q越大,允许停留时间

越短。
颗粒从起始径向位置走完分离区全长(轴向),刚好能沉降(径向)到达鼓壁(对重分散相而言)的临界条件为:
即
或
或
此式的物理意义为:时间常数为

的颗粒在允许停留时间

内完成沉降的**小起始径向位置。起始径向位置大于此值,则此颗粒不能完成沉降。因此,颗粒为x或时间常数为

的颗粒的粒级效率值可定义为半径r与R之间的换装液层体积占鼓内液体总体积的比值:
将式代入式得:
从上式可导出分割粒度

或分割常数

,令G(x)=0.5,得
由上式代入式,可导出管式离心机的生产能力,即
即
其中

,即在重力场下的终了沉降速度
由于式中的
计算不方便,人们利用对数函数的近似值:
得
若定义
则
这就是管式离心机的

常数,决定于离心机的操作参数和结构参数,其梁纲为面积(

)
对于圆锥形转鼓的螺旋卸料离心机
对于柱-锥形转鼓的螺旋卸料离心机
对于碟式离心机
式中
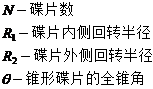
式为

理论的基本表达式,可用来预测离心机的性能,即处理量或分割粒度。预测的处理量即为对应于分割粒度

的生产能力。小于此流量,分割常数为

的颗粒大部分能完成沉降而被分离醋来;否则,分割常数为

的颗粒大部分不能完成沉降。利用

常数,可对几何和动力想死的离心机(如同一类型的离心机)进行操作性能比较,或对同类型离心机作比例放大。设

或

保持不变,则由式可得
注意,不同类型的离心机之间的“横向”比较或比例。
第三章 沉降离心机
沉降式离心机工作原理
离心机的长度和生产能力(进料量)要求固体颗粒有一**小沉降速度,称需要速度,否则固体颗粒会随液体一起溢出。同时,物料的特性及离心机的转鼓半径和转速决定了固体颗粒的有效沉降速度,即有效速度。
3.1.1.需要速度
沉降式离心机简要操作过程为:当转鼓旋转时,物料附于转鼓内壁形成液环,称液池;假设液池中夹杂量很少,固体颗粒一旦沉降**转鼓壁就被卸去;另外,假设固体颗粒进入离心机后沿池深h均匀分布并沉降,而当颗粒沉降时,它必须通过h/2的径向距离。
为保证固体颗粒不随液体溢出,颗粒的滞留时间t给定一个有效沉降时间的上限。设物料在转鼓内柱形流动,则:#p#分页标题#e#
t=L/U二L(A/Q) (1)
式中,L为进料口**溢流口的距离(离心机沉降部分的长度),U为总体流速,由进料量Q(体积流量)和液环截面积A确定。已知颗粒沉降所需要的高度和滞留时间,为保证颗粒被卸去,则颗粒沉降的需要速度为:
V
s(req)= (h/2)/t=(1/2)(h/L)(Q/A) (2)式(2)表明了沉降式离心机与普通重力沉降器的等效性。因LxA是液池的体积,h是池深,故LxA/h近似为液池的“截面积”。在沉降过程中,颗粒通过该面积降**转鼓壁。因此,式(2)即为沉降表面积除以进料量,是沉降方面很常见的公式。
3.1.2有效速度
斯托克斯(Stokes)公式是沉降方面**有用的关联式。该式导出了单个颗粒在粘度为μ的无限流体介质中的临界沉降速度,颗粒的净重(扣除浮力)与粘性阻力平衡。该沉降速度V
s为:
V
s=(△ρ/18μ)gd
2 (G/g) (3)式中:d---颗粒直径,m
Μ---粘度,kg/m·s
△ρ---颗粒与流体的密度差,kg/m
3
g一重力加速度,m/s
2,取9.8
G/g由下式确定:
G/g= /g (4)式中:---转鼓转速,r/s
---转鼓半径,m
式(4)为离心加速度与重力加速度的比值。对于重力沉降,比值为1,对于离心沉降,该比值取决于转鼓半径和转速。若直径1μm颗粒在水中重力沉降,颗粒与水的密度差大约5%,则其沉降速度相当小,仅为0.0001cm/s。如果该颗粒在转鼓转速为3000r/m,直径为60.96cm的离心机中沉降,则离心加速度G约是重力加速度的3000倍,由式(3)得其沉降速度为0.03cm/s。该有效速度为工业生产的实际值,大于前述的0.05cm/s的需要速度。
3.1.3需要速度和有效速度的合成
令式(2)等于式(3)并整理,得Q=2V
s(lg)() /g)(LA/h) (5)式中,V
s(lg)为重力沉降速度(称Stokes沉降速度);为转鼓和液池的平均半径。式(5)表明,沉降式离心机的进料量随重力沉降速度,离心作用强度G/g和沉降表面积的增大而增大。对对转鼓为圆柱形的离心机,其沉降表面积A和池深h为:
A=π(-) (6a)
h=- (6b)
式中,和分别为转鼓和液池的半径。将式(6)代入式(5),得
Q=2V
s(lg)×(/g)x2πL (7)
Q=重力沉降速度x G x表面积
上述关系精确地基于极限轨迹原理和斯托克斯定律。对于不同几何形状的离心机,同样可导出该关系式,总之,进料量与颗粒沉降特性,G和表面积有关。式(7)与实验(如现场试验)存在着差异,这是因为公式中未考虑综合因素。其中二个主要因素是:(1)复合向心力的作用,颗粒大小分布,滞沉降和颗粒形状,(2)流体动力学的作用,对连续式离心机应值得考虑。
沉降式离心机
3.2.1单鼓式沉降离心机
1.撇液式离心机
机构:如图所示,撇液式转鼓离心机主要有转鼓(长径比约为0.6)、撇液管和刮刀组成。
工作流程:进料料液由上部引入,加到鼓底处。清液通过溢流堰溢出。靠近沉淀层的清液由撇液管吸出。固体的排出决定于其流动性。软的或塑性固体在全速转动时由撇液管吸出。粗的或纤维型固体用刮刀在低速刮下,然后经鼓底出口落下卸出(鼓底开口)。
由于液料加入后往往不在整个流通截面上均匀流动,而趋向在自由液面附近的液层流动——表面流动。这会导致流速加大,停留时间缩短,对分离不利。因此,有的设计在转鼓内加了特殊的挡板,限制这种流动。
撇液式转鼓离心机通常用于在质量浓度为3%~5%料浆的脱水和从废液中回收固体,处理量6~10m#p#分页标题#e#
3/h,转速范围450~3500r/min。
2.管式离心机
结构:如图所示,管式离心机主要结构特点为细长无孔转鼓(直径70~160mm,长径比4~8),悬挂于离心机上端的橡胶挠性驱动轴上,其下部与中空轴连接,中空轴**于机壳底部的导向轴衬内。
工作流程:物料经下部一固定的进料管进入底部空心轴,而后被导入鼓底,由于鼓内十字形挡板的作用,加速**转鼓速度发生沉降。管式离心机可用于液-液分离和固—液分离。对于液—液分离,轻液通过驱动轴周围的环形挡板环溢流而出,重液则从转鼓上端排除。转鼓上端装有可更换的不同内径换装隔液环来调节轻重液的分层界面。由于液—液混合物没有流动性问题,因此由于液—液分离的管式离心机为连续操作。对于固—液分离,由于固相沉淀物流动性差,只能采用间隙式操作。固相出口必须关闭,停车拆下转鼓进行清理。否则,固体越积越多,流通截面减小。流速加快,停留时间减小,会降低分离效率。
为了避免过分频繁的清洗,管式离心机通常用于处理含固量小雨1%的悬浮液。在生产过程中为了保持连续处理,采用两台离心机交替使用。
优点:1平均允许停留时间要比同体积的转鼓式离心机的长;2分离能力大;3结构紧凑和密封性好;
缺点:1容量小;2分离能力较碟片式的低;3固—液分离只能为间隙操作。
3.螺旋卸料式离心机
1螺旋式卸料离心机的形式
螺旋卸料式离心机,根据主轴方位分为卧式和立式两类,但以卧式为主,简称“卧螺”;按功能或用途,螺旋卸料式离心机可分为脱水型、澄清型、三相分离型和分级型等几类;按转鼓内流体与沉渣的流动方向可分为逆流式和并流式两种。
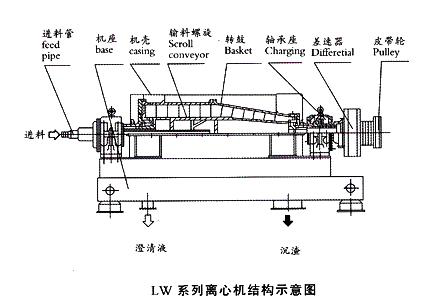
螺旋卸料式离心机,转鼓圆锥形或柱—锥形,螺旋卸料器;进料管为螺旋输送器的空心轴,在此空心轴上某一轴向位置(偏向底流口)开有进料口;溢流口(若干个溢流孔)在转鼓的大端,底流口(排渣孔)在转鼓的小端。
立式螺旋卸料离心机其结构特点为整个机体为立式,上部驱动,下面进料、排渣、上面排液;澄清区和干燥区的长度可通过环形溢流堰调节;滤饼可洗涤;离心机装有转矩超载安全装置,以保护减速器。电机通过皮带轮带动转鼓转动,转鼓再通过行星齿轮减速带动螺旋输送器转动。物料通过加料管进入转鼓中部,液体沿螺旋上升流动,由调整液层厚度的可调式溢流挡板孔溢出。沉降于转鼓内壁上的沉渣由螺旋输送器推向卸料口卸出,立式螺旋卸料式离心机的型号及主要技术参数如表7-3所示。
立式螺旋卸料式离心机适用于分离含固相颗粒5μm以上的悬浮液的脱水和固相含量少的悬浮液的澄清,特别是固体颗粒浓度即颗粒变化范围较大、固体相对密度较大的悬浮液的分离。如淀粉悬浮液脱水,回收植物蛋白,分离可可、咖啡、茶等虑浆,及鱼油去杂=鱼肉制取等。
2螺旋卸料式离心机的主要部件
转鼓 转鼓是螺旋卸料式离心机的关键部件之一,其主要结构参数包括转鼓直径D、转鼓长度L、转鼓锥角θ、转鼓的溢流直径D
u。转鼓直径D是转鼓的**大内壁直径。转鼓长度L是沉降区长度L和脱水区长度L之和。这些参数直接影响到螺旋卸料式离心机的分离能力、处理能力和输渣能力。
转鼓有转鼓体、大端轴颈和小段轴颈用止口噢诶和螺钉连接而成。转鼓筒体可选用碳钢、不锈钢及玻璃钢。如分离因数高又要求耐腐蚀,应选用高强度不锈钢喉钛合金材料制作。
转鼓大端轴颈的凸缘上开有溢流口,分离液经此流出转鼓。溢流口直径决定液池的深度,直接影响离心机的分离能力和生产能力。为提高离心机对物料的适应性,溢流口径位置应可调。
转鼓小端的出渣口形式和耐磨性十分重要。出渣口与渣的摩擦强度比任何部分都大,因此易于磨损,为保护出渣口,通常采用喷涂耐磨材料后可拆换的耐磨衬套。转鼓小端出渣口6外装有左套环2和右套环3,两套环由螺钉4夹紧在转鼓1上,并使出渣口6于组合出渣口7同轴,出渣口6内装有耐磨衬套5,衬套5可选用淬火钢、钨合金等耐磨性好的材料制造。衬套中套的环状凸缘8装在沉孔9中,以防止衬套做轴向运动。当衬套局部磨损后,可拧松螺钉4、衬套5转动一定角度,使未磨损的部分工作,当衬套磨损严重不能再使用时,拆下套环2和3更换之。
螺旋输送器 螺旋输送器的作用是利用螺旋与转鼓间的转速差将沉降在转鼓壁上的沉渣输送到转鼓小端的出渣口排出。连续整体螺旋主要部件由做轴颈、螺旋筒体和有轴颈组成。左、右轴颈上装有轴承,通过它们装在转鼓的左、右轴颈内,以实现螺旋与转鼓的同时同向但有速度差的旋转运动。右轴颈上的事一对止推轴承以承受螺旋推渣时产生轴向力。左轴颈童工花键轴将差速器和螺旋连接起来。螺旋卸料式离心机工作时,特别是当物料中有泥沙甚**是沙粒存在时,例如分离矿料时,螺旋叶片会产生磨损,当物料有腐蚀性时尤甚。螺旋叶片磨损后,通常使螺旋的分渣能力降低。因此,要求螺旋叶片具有一定的耐磨性。螺旋叶片的本体材料一般与转鼓相同,现有三种方法来增加螺旋叶片的耐磨性。①在叶片易磨损部位堆焊硬质合金(如钴铬,古镍合金、碳化钨等,以碳化钨的耐磨性**好)。②采用表面喷涂技术,即在叶片易磨损部位喷涂耐磨材料如碳化钨等。喷涂的方法有火焰喷涂、电弧喷涂、等离子喷涂、爆炸喷涂等。爆炸喷涂形成的涂层结合强度大、表面硬度高(如喷涂碳化钨和钴混合粉末时硬度HV=1300)、光洁度好、加工温度低(一般在200°C以下),故螺旋变形小。③采用可更换的耐磨扇形片,即用可装拆的耐磨扇形片作为螺旋外圈。#p#分页标题#e#
③螺旋卸料式离心机的工作过程
电动机通过带动转动传动装置带动转鼓旋转。行星差速器的输出轴带动螺旋输送器与转鼓作同向转动,但转速不同,其转差率一般为转鼓转速的0.2%~3%,以产生螺旋输送卸料作用。物料从右端的中心料管经进料孔进入转鼓。在离心作用下,转鼓内形成了一环形液池,重相颗粒离心沉降到转鼓内表面形成沉渣,由于螺旋叶片与转鼓的相对运动,沉渣被螺旋叶片输送到转鼓小端的干燥区,从排渣孔12连续甩出,澄清液从溢流孔11流出,经机壳的排液室排出。因此,螺旋卸料式离心机可连续工作。调节溢流板溢流口位置、机器转速、转鼓与螺旋输送器的转速差和进料速度,就可以改变沉渣的含湿量和澄清液的含固量。
螺旋卸料式离心机可用于回收晶体和聚合物、城市污泥及工业污泥脱水,也可用于分级操作。例如,用于高岭土分级、去粗,10μm以上100%去除,2μm以下的产品达80%~85%。用于污泥脱水时,只能用大分子量聚合电解质作为絮凝剂时才能将污泥的含水率从95%以上降到60%~70%。
④螺旋卸料式离心机的特点
螺旋卸料式离心机与其他离心机比较,能自动、连续操作,单机生产能力大;对固体颗粒粒度和浓度的变化不敏感,因此,可以分离含固相颗粒粒度0.005~2㎜、固相浓度1%~50%(重量)的悬浮液;分离因数、转鼓长径比涉及范围大,转鼓液池深度可调,因此,对物料的适应性强,应用范围广。
但是螺旋卸料式离心机的沉渣含液量较高,虽然能对沉渣进行洗涤,但洗涤效果不好。另外,螺旋卸料式离心机转速高,转动件加工精度高,结构复杂,制造成本高。
⑤螺旋卸料式离心机的主要应用
脱水 对易分离物料,可以得到含液量较低的固体。对那些用过滤机和过滤离心机不可经行分离或分离效果极差的物料,可以通过选用适当工艺参数和结构参数的螺旋卸料式离心机来完成分离过程。
澄清 微细颗粒悬浮液可以采用分离因数高、长径比大的螺旋卸料式离心机来完成。例如活性污泥,经絮凝剂处理后,用螺旋卸料式离心机分离,分离液的固相含量完全达到排放标准。
轻固相分离 即密度比水小的固体颗粒的分离。
液—液—固三相混合物的分离 固相浓度大于14%的液—液—固三相混合物用碟式分离机难以分离,一般用液—固和液—液两个分离过程,而用螺旋卸料式离心机可以实现三相一次性分离。
固相颗粒粒度分级,可采用适当的分离因数和合理的结构来实现。
⑥常用的螺旋卸料式离心机
脱水型卧式螺旋卸料式离心机 这类离心机风分离因数一般小于3000,常采用处理易分离物料、即固体颗粒的自然沉降速度较快、沉渣较容易分离的悬浮液,如洗煤厂的浮选精矿和尾矿、聚氯乙烯、聚乙烯、聚乙烯醇、淀粉、食用油渣的混合液等。转鼓呈锥形或柱——锥形,转鼓长径比较小,一般为1~2,直径比较澄清型卧式螺旋卸料离心机大,转鼓锥角20°~36°。锥角大,脱水分离因数高,有利于沉渣脱水。另外,转鼓内液池浅,一般池深h与转鼓半径R之比为0.10~0.20.螺距较大,一般是螺旋直径的1/2~1/5,以提高沉渣的输送能力。
澄清型卧式螺旋卸料式离心机 这类离心机的分离因数一般大于3000,用于固体颗粒细微、滑腻的悬浮液(如活性污泥)等的澄清,特点是转鼓呈柱—锥形或双锥形,转鼓长径比一般为2.5~4,转鼓锥角常小于20°(用于活性污泥处理时,转鼓锥角小于8°,否则排渣困难)。转鼓内的液池深度较深,一般h/R=0.2~0.4,螺旋输送器的螺距较小,一般是螺旋直径的1/5~1/6,有利于输送滑腻的沉渣。
表7-5为Sarplers公司的卧式螺旋卸料离心机的技术参数。该离心机的直径从150mm的小型机到家大于1m的超大型机。该离心机可用于淀粉乳脱水、果汁纤维分离、动植物油的净化、大豆蛋白的脱水、味精的脱水、厨房用油的净化等。
3.2.2多鼓式沉降离心机
如前所述,多鼓式沉降离心机转鼓的排列为径向排列。这样,不但使空间利用率高,而且可以提高离心机的性能。单鼓式离心机内的物料径向厚度达,要沉降的颗粒距离长,导致生产能力小或效率低。径向排列多股式离心机由多个不同直径的转鼓同轴安装,形成多个分离室(故也称多室式离心机),使颗粒**大沉降距离从单转鼓的整个液层厚度减为鼓于鼓之间的径向间隙,大大减小了要颗粒沉降的距离,从而可显著提高离心机的性能。缺点是结构较为复杂。
分局离心机内无聊的流动形式,径向排列多鼓式沉降离心机有两种类型:一种为并联式,每一个分离式独立进、出料;另一种为串联式,物料shou先加到内分离室,然后逐级向外流动、分离。
(1) 多股并联式沉降离心机
① 三转鼓沉降离心机
结构:三转鼓沉降离心机,亦称三转式离心机,有三个不同直径的转鼓组成。
进料:由一个进料歧管将进料分别输给三个转鼓。
排料:三个转鼓独立排料。
优点:减小沉降距离,增加停留时间,顾客在较低转速(650r/min左右)下工作。
② 碟式离心机
结构:碟式离心机的转鼓内有一组(有100或100个以上)锥形碟片,间距0.4~3mm,
锥角70°~100°。碟片上沿锥面周向有3个均布的进料孔(哦、孔径6~13mm)和3条均布的筋以此形成碟片间隙。对于奶油分离机,筋高0.3mm~0.4mm;对于酵母分离机,筋高0.8~1mm。碟片与转鼓同轴安装,以相同的转速旋转。卫士转鼓容量**大,一般转鼓高度与直径之比为1。碟片外径与转鼓**大内径之比为3/4时,可得到**佳性能。#p#分页标题#e#
工作流程:进料沿转鼓中心引入(轴向进料),以薄层在碟片间沿径向向内流动,在离心力的作用下,颗粒或重相沉积在锥形碟片下表面上,并向下向外滑动,**后甩到转鼓壁上;液体或轻相向中心流动,以溢流流出。由于碟片将分离室分成若干层,缩短了颗粒所需完成沉降路程,从而缩短了沉降时间,加速了离心分离过程。这就是采用碟片的原因。
碟片离心机可用于固液分离和液液分离。用于固液分离时,固体颗粒的粒度范围为0.5~500μm。由于液液分离时,可以来分离乳化液。由于液液混合物中常常含有固相,因此,碟式离心机用于固液分离和液液分离时都有排渣要求。
根据固体卸料方式,碟式分离机有人工排渣、环阀排渣和喷嘴排渣三种不同的结构形式。不同机型的碟式离心机,随被分离物料的性质和分离要求的不同,分离效果和处理能力也不同。碟式离心机的基本技术参数有转鼓直径、转速、当量称将面积等。不同碟式离心机的基本蚕食如表7-6所示。
人工排渣型 亦称固体保留型转鼓结构简单,间隙操作,人工卸料,用于处理固体浓度小于5%的悬浮液。固体的容量为5L~20L,常用于牛奶脱脂。固体保留型碟式离心机直径约为150~300mm,转速一般为5500~10000r/min。
喷嘴型 转鼓为双锥体,椎体周边均匀分布的排渣喷嘴,能连续排渣,从而能连续操作。这种转鼓能提供较大的固体存留空间。为了避免发生沉积固体积累或堵塞现象,并能获得较浓的泥浆,喷嘴的数目和直径需要精心的设计(喷嘴数一般为12~24,直径为0.75~2mm)。底流分率一般为5%~50%。这种离心机可用于粘土、高岭土、颜料、酵母、油、焦油、湿法磷酸的脱水、澄清,也可用于羊毛脂分离提取等,喷嘴排渣碟式分离机用于浓缩过程中,浓缩比可达5~20。这种分离机适用于处理固体颗粒粒度0.1~100μm、体积浓度6%~12%的悬浮液,**大处理能力可达300m
3/h。因通过喷嘴的流体流速很大,喷嘴需要耐磨材料如硬质合金、刚玉和碳化硼等制成。
环阀排渣型 环阀排渣型碟式离心机又称自动 排渣或活塞排渣碟式分离机。转鼓内有与其同轴的排渣活塞装置,周边有若干个一定圆弧长度的环槽排渣口。这种排渣口能比圆形排渣口排更粗、更粘稠的沉渣。根据固体沉积厚度,液压作用,活塞可上下移动,自动启闭排渣口—断续自动排渣,也可以由定时器来控制排渣口的启闭。
环阀排渣型碟式分离机为固体卸出型,分离因数5000~9000,适于处理固相颗粒0.1~500μm、浓度2%~6%、固液相密度相差大于0.01g/cm
3的悬浮液,亦可用于处理在剪切作用下容易破碎或解聚的固体,还可使不已压实的固体得到较好浓缩脱水,以及各种汁液的澄清,等等。**大处理能力40m
3/h。
按液压作用方式,环阀排渣型碟式离心机可分为间接泄压式和直接作用式两种。下面以间接泄压式为例介绍环阀排渣型碟式离心机的基本结构及工作原理。
间接泄压式环阀排渣型碟式离心机专门的泄水阀使活塞下腔内的水迅速写呀,活塞在上下操作水腔室内液压差的作用下,向下移动,经行排渣。泄水阀可径向或轴向安装。
转鼓液封侯可开始加料,由于离心力作用,被分离的物料对活塞产生一个大的下推压力。但由于活塞控制腔的水系作用在一个较大的半径上,故操作水对活塞上推力要比物料产生的下推力大,使活塞能牢固控制地压紧封圈,吧物料密封在转鼓内经行操作。造物料分离过程中,控制腔要进入小量补充水,以补充因活塞密封圈密封不严的微小泄露,以及因转鼓内物料温度较高引起水蒸发而损失的水,从而保证分离过程中有稳定的操作水腔的压力。
当分离一段时间后,沉渣聚集于转鼓沉渣区达到一定量时(沉渣延及碟片大端直径)从分离液质量变差或其他方法液叛变出。这是需要进行排渣过程。排渣时,先关闭加料阀,停止加料。转鼓内加水把转鼓内的轻液排完。液压进水装置将操作液通过通道进入泄水阀的小活塞3内,此处半径大于控制腔的半径,产生的离心压力比控制腔处的大,所以操作水推动小活塞项转鼓中心方向移动,使小阀头2打开一个缝隙通道口,控制腔内的水便通过从口,从排水口排出,转鼓内沉渣和料液的下推压力使活塞下落,打开排渣孔,沉渣遂在离心力作用下派驻转鼓外。
(2) 多股串联式沉降离心机
结构:多股串联式沉降离心机在一个密闭的转鼓内分为阮干个同轴圆筒分离室,一般分为三个分离室。
工作流程:料液shou先从中间加入到**里面的分离室,进过**次沉降后,溢流到外层分离室进行沉降,依次进行下去。
优点:除了上述三鼓式沉降离心机的优点外,多股串联沉降离心机还有一个分离作用。由于离心力与转鼓直径成正比,所以分离因数从里向外逐渐增大。因此,里面转鼓上沉积的为粗颗粒,外面转鼓上沉积的为细颗粒。